Introduction
A small army of drones is now successfully dominating Railway operations worldwide with their perceptions from the sky. Drone technology has fundamentally opened up distinct opportunities for Railway operators, promising safety and reliability alongside their trustworthy assistance. Elements of transportation, such as rail infrastructure, are being inspected rigorously via UAVs to assure safe experiences for passengers and freight.
Drones in the Railway industry have become a piece of necessary equipment for stable railway inspection systems. They are employed to monitor significant railway infrastructures such as high-voltage electrical lines, railway catenary lines, and even tracks and switching points. With drone technology’s assistance, extensive drone imagery is obtained, to magnify the process of defect detections, crack detections, and additional dangers quickly. The more frequent the inspections are the higher railway security, dependability, and scheduled performance there is. Higher productivity would, in return, reduce expenses and warrant overall productivity from the industry
Drones for Railway Inspection
With Drone Technology by the railway sector’s side, the heightened safety of workers’ is now praiseworthy. Railway operations that earlier demanded workers to indulge in hazardous situations for inspections are now no longer a concern with the influx of drones. The integration of premium drones, advanced sensors, high-resolution cameras, Artificial Intelligence, and Machine Learning have made seizing real-time information and smart data analysis a reality for this transportation sector.
Rail Track Monitoring Through Drone Imagery
As per railways accidental statistics, significant derailments are said to occur solely due to human incompetency or irregular and incorrect monitoring systems. Traditional railway inspection systems incorporated workers to inspect railroads through unreliable automated vehicles. The existing practices comprise methods like electromagnetic inspection, eddy current testing, ultrasonic systems, and optical techniques to implement numerous inspection operations in the railway industry. With the advancement of technology, the drone industry uses the following procedures to capture specific inspection data from railroads and related infrastructure:
- Data Acquisition – This initiation stage of acquiring aerial images is said to be one of the most crucial tasks for computer vision applications. High-quality drone imagery of railway infrastructure is a fundamental element in maintaining a sustainable track inspection system. Due to this very reason, Equinox’s Drones employ well-established drones like the DJI Phantom 4 PRO for drone surveys in the railway industry. The DJI Phantom 4 PRO is outfitted with a 4k camera, can document videos in FHD and HD, and is proficient in delivering HD 1280X720 and 24/25/30p @30mbps recording models.
- Data Pre Processing – Any drone data accumulated through railway inspections pose their own set of hurdles, commanding the need for alterations, calculation of ground sample distance, extraction of frames from videos, and other such pre-processing requests. Using advanced software such as Pix4D, 3DF Zephyr, and RealityCapture, Equinox’s Drones favourably reconstructs the data to make them well-suited for further stages. Interferences like harsh weather conditions pose a threat to the quality of images captured since their illumination, noise level, etc. are significantly changed.
- HSV Color Extraction –
HUE, SATURATION, VALUE Hue, Saturation, and Value, popularly known as HSV, is an alternative colour space model of the RGB model. It interprets the RGB colour model in cylindrical coordinates and expresses colours according to their Hue (actual colour), Saturation ( volume of grey), and Value (illumination). It’s perceived that images captured through drones have differing colour contrasts due to unsuitable weather conditions or when caught at varying times during a day. Drone images are obtained and converted into HSV models to overcome the influence of weather restrictions and improve the overall quality of the railway inspections.
- Track and Edge Detection –
TRACK AND EDGE DETECTION Before the railway tracks are distinguished from the edges during ‘edge detection’, small connected pixels are removed with the assistance of numerous software. Through softwares such as Pix4D, 3DF Zephyr , and Reality Capture, a defined edge of the track is determined to subdue the probability of elements other than the railway tracks detected. This process is known as track detection. Edge detection systems are administered to distinguish the railway tracks from its background and surrounding details.
- Gauge Measurement –
GAUGE MEASUREMENT Ground Sample Distance, popularly known as GSD, is a critical concept to grasp since it can influence the precision of railway inspections done by the drone operator. GSD charts the distance among pixel centres from the camera sensor to the actual distance on the ground, subject to the height and features of the drone camera. Data engineers and even drone specialists can estimate GSD through calculating senor size (CCD) of the drone, along with other data such as focal length, UAV flying height, etc. Estimate GSD in the following manner:
CCD Pixel size = Width of sensor in cm/ Image width in pixels
GSD =(Hg/Ck) ×CCD pixel sizeHere,
Hg=Flying height of the drone
Ck=Focal length of drone camera
Discovering damages in railways with the support of drones has marked a new beginning for the industry. Earlier, defects that compelled humans to monitor are now supported with supplemental platforms such as Artificial Intelligence and Drone Technology. It is claimed that the rail, sleeper, and fastener are some of the most significant components to scrutinize for defects on railway tracks. Deformed rails and broken sleepers are a few examples of potential dangers, and if not resolved soon, they could cause severe damage. All methods mentioned above ensure that defects such as cracking, peeling, scratches, folds, broken rails, scars, etc. are accurately recognized. UAVs have evolved to fill gaps of inspections of conventional railway inspection systems and developed the operation with fewer interruptions, more effectiveness, and efficiency.
You may also like
Methods of Uav Infrastructure Inspection
Camera-Based Sensing and Image Processing
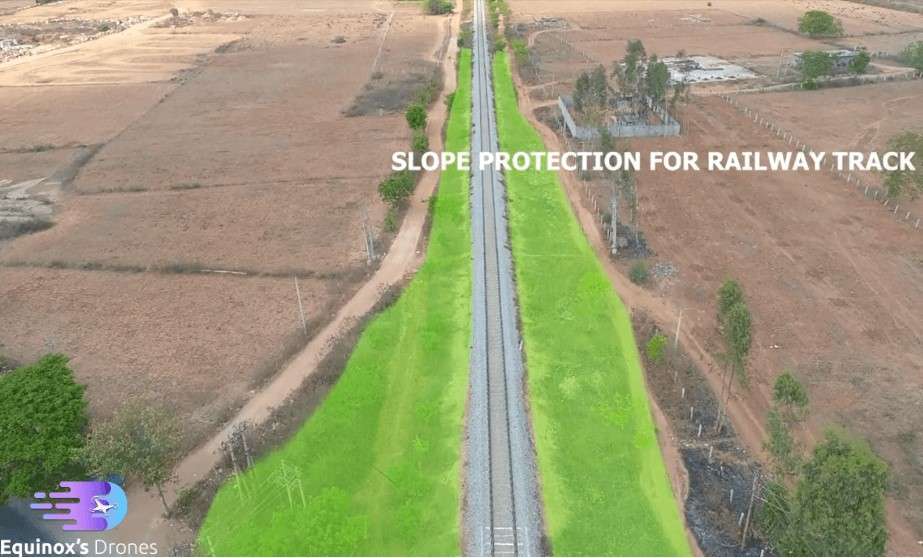
Unmanned Aerial Vehicles (UAVs) naturally demand sensing capabilities. Significant sensors such as ultrasonic sensors, colour/ thermal/infrared cameras, or even laser rangefinders are equipped with drones to procure precise drone data. Less expensive drones are commonly furnished with colour cameras, after which data can be obtained through various computer vision methodologies. With specific reference to UAV navigations, the following points are perceived:
- Feature detectors and descriptors are frequently adopted for object detection purposes
- Optical flow techniques are employed to recognize motion in environments
- Visual servoing is applied to transpose image frame motions into UAV displacements
- 3D reconstruction techniques are utilized for navigation and mapping activities
Every technique is appropriate and reliable, contingent on the environments and nature of objects targeted.
- Object Detection – The fundamental mechanisms for object detection and tracking includes feature detection and description algorithms. This method can be utilized to extract the drone’s position, along with more insight into its motion. Feature Detection identifies the areas of interests in photographs, labelled as either edge, corners, or blobs. On the other hand, descriptors are applied to coordinate a specific feature in two photos. An object motion tracking system is comprehensive only with a combination of detectors, descriptors, and matching techniques. Feature detectors are valuable for identifying targets like buildings or objects, or even references like linear structures that are necessary to follow.
- Optical Flow Techniques – Optical flow is a primary technique that concentrates on ascertaining motion from imagery. In other words, optical flow is the pattern of the apparent movement of objects, surfaces, and edges in a 3D environment. Optical flow detection can be achieved with optical mouse sensors. However, this detection method is usually time-consuming and is often fitting for near-hovering operations of UAVs.
- Visual Servoing –
Visual servoing is a technique that incorporates guiding camera motions with the assistance of visual data. In specific to UAV navigation, visual servoing approaches allow transforming image frame motions into real-time content. This technique is prevalent in situations of flight inspections near traffic signals, gas pipelines, and even while scanning buildings.
- 3D Reconstruction Mapping – In computer vision, 3D reconstruction is the method of capturing real objects’ shapes and appearances by either active or passive techniques. However, this method still poses its own set of challenges. Most of the vision algorithms are restricted in use due to the illumination of the situation, pattern models, and captured objects’ motion. This method also extends processing time and cannot scale data of 2D images, leading to the requirement of additional tools like sensors to acquire reliable information.
Benefits
- Safety – Engaging with drones for railway inspections has developed the sector’s productivity and level of safety. The transition toward an automated future for the railway sector has manifested various benefits that can soon become cost benefits for regulators. Given that trains are scheduled with the utmost regularity along most railways, sending a worker to inspect the tracks in any specially equipped vehicle can result in catastrophic loss. With this rising fear, the necessity of drones in the sector has grown. UAVs do not utilize equivalent space like trains and remain above vital operations throughout their inspection activities. This way, organizations can cautiously and precisely inspect railway infrastructure without having to compromise on worker safety.
- Time – Saving One of the most prominent yet most significant advantages of drone inspections is that they can fly over railways, empowering organizations to save overall time. Railway firms can preserve time since UAVs on-site can accumulate data from multiple railways as they scale into higher altitudes, simultaneously visualizing 3-4 tracks at a time. Drone Technology and Machine Learning also enable them to perform the task independently without needing any human assistance. Data acquisition becomes smart, immediate, efficient, and repeatable with drones.
- High – Resolution Data – Premium drones with high-resolution cameras can provide crucial data in no time for railways. Once the drone data is obtained, it can be processed through advanced software to identify defects in railway infrastructure using change detection techniques or even Artificial Intelligence.
- Reliable – Given that Drone Technology undoubtedly provides detailed information, the railway industry relies on its output massively. The authenticity of data can regularly be confirmed using orthomosaics in case of any doubts. Drone data has become almost every industry’s most trustworthy source of information and enables active decision-making.
- Independent Terrain –
AERIAL INSPECTION Since drones fly in the open air, there are no barriers encountered by UAV operators in the industry. Extra efforts and safety measures must be taken when functioning in a hilly region, rivers, or above bridges. Drones in this sector are terrain-independent. However, it must be noted that land-dependent arrangements are terrain-restricted and require additional effort and administration based on the topography.
- Identifying Obstacles – Since a land boundary can be placed over an orthomosaic, railway firms can recognize land acquisition concerns or any collisions with existing construction projects. During drone surveys, valuable information about the surroundings are gathered, and any interferences recognized can be resolved in time.